Sharpening Chisels

Chisel Angles: A Rule of Thumb is that 20-25 degrees is for paring (pushing), 25-30 degrees is for general all-round work, and 30-35 degrees for heavy work (such as pounding).
Why are bevel angles different?
So the cutting edge lasts longer in use – it’s a compromise. The finer the cutting edge, the finer and faster the cut, and the bevel chosen for specific chisels is based on the tasks they are to perform and the ability of the steel used to hold its edge under those conditions. Paring chisels are ground with shallow bevels, 15 to 20 degrees, for delicate use. Use a mallet on them, and you’ll break down that fine edge quickly and be forced to sharpen too often. Mortise chisels, in contrast, are ground specifically for mallet use and have steep bevels, 30 to 40 degrees or more, but in turn, don’t function as well for paring. Bench and firmer chisels are compromises to do both and are found with 20 to 30 degree bevels, bench chisels generally on the shallow side of that range for more efficient paring, and firmer chisels on the steep side of that range for more efficient chopping. It often varies slightly by manufacturer because of the steel each manufacturer uses. There are several factors involved, but generally, the harder the steel used, the steeper the cutting angle must be to prevent chipping the edge. Blades laminated with very hard steel at the cutting edge and soft steel atop like found in some older Western edge tools and most Japanese tools require steeper bevels than non-laminated tools.
Most new chisels aren’t sold with “secondary” or “micro” bevels added to the main bevel’s cutting edge, it’s a matter of individual preference whether they are used or not. A secondary cutting bevel is achieved by raising the chisel handle slightly during honing from anywhere from two to five degrees to add a second small bevel at the cutting edge. The advantage is significantly greater speed in honing the blade, as only a couple thousandths of that blade at the edge actually does any cutting, so why hone the entire cutting bevel? The disadvantage is that the main bevel must be honed eventually, as continued honing of only the secondary bevel will eventually round over the main bevel and require regrinding. Regrinding often shortens the life of the tool by taking off more steel than needed, so why postpone that work by honing secondary bevels? It all has to be done anyway, how and when you do it is your choice. I use secondary bevels on almost all my edge tools, but every third or fourth honing lower the handle and hone the main bevel on the coarse stone to keep it flat, and have gone as long as decades without having to regrind the main bevel in some of them.
Bob Smalser
from
Sawmill Creek Forum: http://www.sawmillcreek.org/showthread.php?40607-Japanese-vs-Western-Chisels/page2
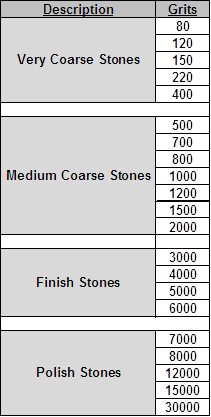
Additional reading.....
A guide to Honing and Sharpening: A step by step sharpening guide
for more links to help you sharpen your chisels